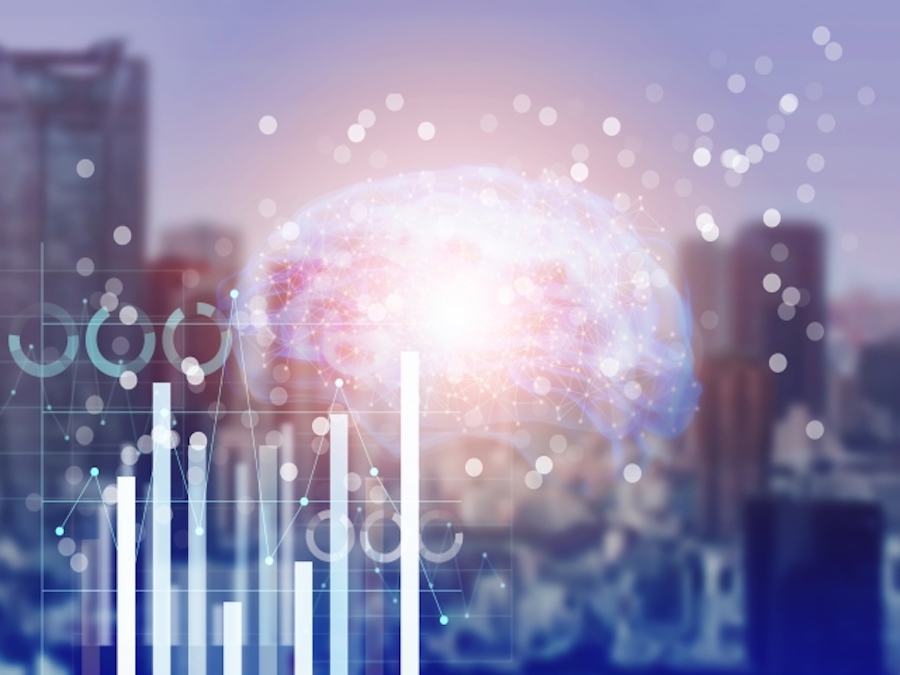
スマートファクトリーとは?IoT時代の効率的な生産システムについて解説
近年、製造業の分野で「スマートファクトリー」という言葉が聞かれるようになっています。
ロボットやAI、IoTといった技術により、生産設備の自動化・自律化の流れが強まる昨今、製造現場における業務の効率化に大きな期待を寄せられているのが「スマートファクトリー」という考え⽅です。
実際に、生産性向上を目的にスマートファクトリーとしてのシステムを導入する企業も増えており、政府もこの「工場のスマート化」を全面的に後押しする構えを見せています。2017年には、経済産業省からスマートファクトリーへの移行に向けたロードマップが発表され、今後スマート化を検討する企業への指針が公的に示される形となりました。
今後の製造業において「スタンダードな工場のあり方」として定着していく可能性の高いスマートファクトリー。今回はその重要性やメリット、導入の際のポイントについて、具体的な導入事例とともに紹介していきます。
目次
スマートファクトリーとは
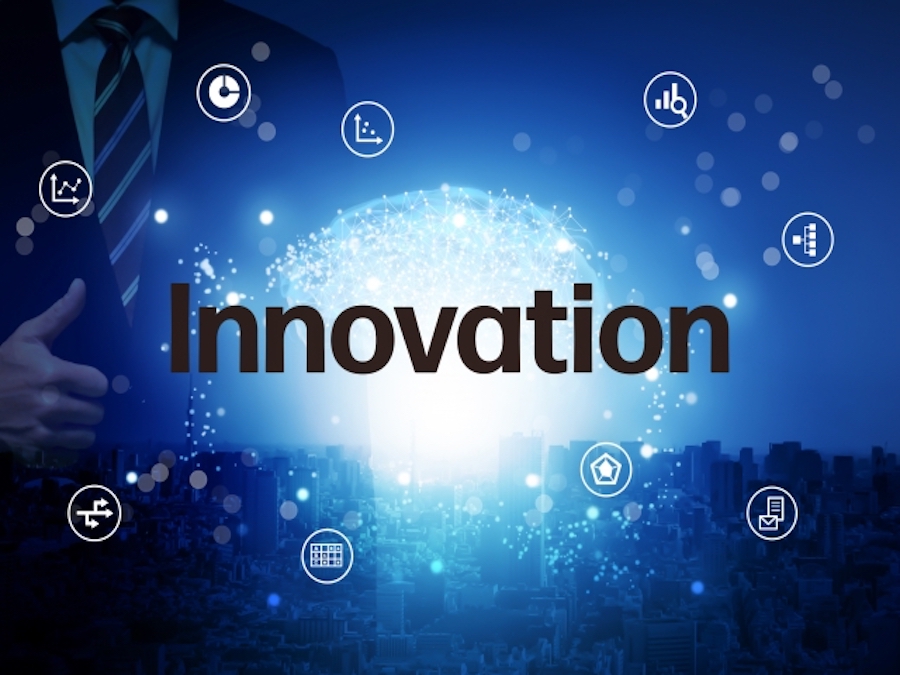
スマートファクトリーとは、ロボットやAI、IoTといった先進技術を導入することで、生産における負担の削減・生産管理の一元化など、多角的に生産性を向上させていく新しい製造業のあり方です。
生産設備そのものにセンシング機能を搭載し、作業データをネットワークで共有するなど、生産プロセスの可視化や部門間の連携強化にとりわけ大きな効果が期待されています。
スマートファクトリーはもともと、ドイツ政府の提唱する「インダストリー4.0」というコンセプトに端を発する概念です。インダストリー4.0は日本語で「第四次産業革命」にあたり、「生産プロセスのデジタル化・IT化が、製造業界の生産様式を飛躍的に改善する」という壮大なビジョンを表す言葉になっています。
この「第四次産業革命」が実現される過程で、それぞれの工場はAIやIoT技術をフルに活用した「スマートファクトリー」の形へと移行していく、ということが見込まれています。
スマートファクトリーにおいて目指されているもの
スマートファクトリーの狙いは、「先進技術で人間の負担を減らす」ことだけではなく、「マスカスタマイゼーションの最適化」という点にもあります。
マスカスタマイゼーションとは、付加価値の高いカスタム製品を大量に生産するシステムを指す概念です。その実現には「多くの品目を少量ずつ生産する」「複数の製品を混在させながら生産する」といった複雑な生産工程を連携させる必要があります。
たとえば、スマートファクトリーへの移行により、生産ラインと受注システムを連動させ、生産設備が自律的に最適な生産管理を行うシステムを構築できれば、受注から製造までのプロセスを隙間なく接続できるでしょう。その他、受注と購買、開発・設計など、さまざまな部門をつなぎ、それぞれの現状がリアルタイムに工程に反映されるような、統合的なシステムも実現しうるのです。
スマートファクトリーにおいて目指されているのは、このように「生産設備によって、業務の垣根を超えた最適な生産工程を自律的に実現できる」形だと言えるでしょう。
⽇本でスマートファクトリーの導⼊が必要な理由
以上のように、スマートファクトリーには生産工程の最適化にあたって多大な貢献が期待されており、とりわけ現在の日本社会において導入される意義は大きいと言えます。以下、3つの観点からその意義を解説していきます。
(1)「労働人口」の問題
超高齢化が進む日本社会において、今後労働人口は減少の一途を辿ることが想定されており、企業にとって人材の確保は困難な課題となっていくでしょう。そのような情勢のなか、就業人数を削減しつつも生産性を維持・向上しうるスマートファクトリーは、安定した経営を続けていくための最適解となりうるものです。
(2) 「技術の継承」という問題
製造業において、生産技術の習得に時間を要する品目は、付加価値の高さから見ても重要度の高いものです。習熟度の差は品質の差として表れるため、付加価値の高い製品を安定して供給していくためには「技術を正確に受け継いでいけるシステム」が必要となります。
労働人口の減少が見込まれる日本において、スマートファクトリーは「従業員の技術の均一化」という面でも効果が期待できます。作業工程をモニタリングし、ミスが生じやすいポイントを浮き彫りにすることも可能ですし、さらには模範的な作業者の動きをデータとして解析し、マニュアルとして共有したり、AR技術を用いた研修制度を導入したりと、「従業員の教育」という観点からも大きな意義を持つでしょう。
(3)「縦割り型の組織構成」の改善
各自の権限を厳密に区分する官僚的な組織構成は、いわゆる「お役所」だけではなく、日本の多くの企業にも該当するものだと言えるでしょう。こうした縦割り型の構成は、従業員がルーティンワークをこなすうえでは効率的ですが、「組織の柔軟性」という面で、部門間の連携が必要な場合の時間的ロスが大きく、臨機応変な動きを困難にしてしまいます。
開発・受注・購買・生産といったプロセスをシームレスに連動させうるスマートファクトリーは、ルーティンワークの安定化・効率化はもちろん、状況判断の自律化による柔軟な対応力をもたらしてくれるでしょう。
スマートファクトリーのメリット・デメリット
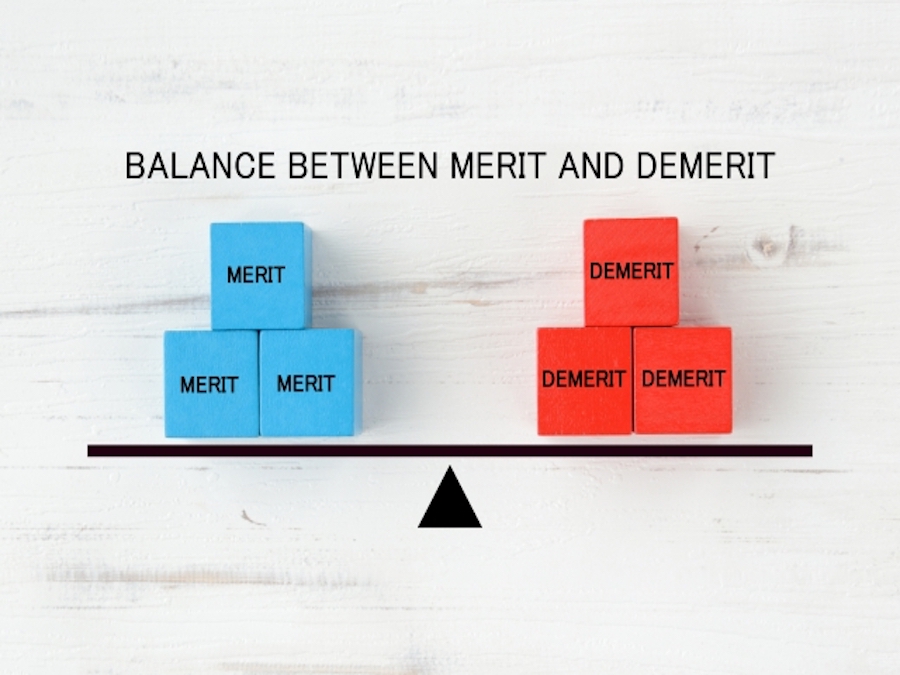
スマートファクトリーへの移行は、産業革命にも例えられるほど、抜本的な変化が生じうるものです。まったく新しいシステムの構築により、さまざまなメリットがもたらされる改革には、リスクもつきものです。
ここでは、導入を検討している方への判断材料として、スマートファクトリーのメリットとデメリットを紹介していきます。
スマートファクトリーのメリット
(1)状況の可視化・管理の一元化
生産設備にセンシング機器を設置することで、生産ラインの細かな稼働状況などがデータとして把握できるようになります。そのような工程データと、受発注の状況、さらには顧客情報など、多岐にわたる情報を連携させ、解析ツールなどでグラフや表に落とし込めば、誰もが全体の状況を一目で確認でき、複数部門におけるデータを統合し、生産プロセスを一元的に管理することが可能となります。
(2)品質の安定化
ロボットやAIの導入により、品質にバラつきがなくなることが、スマートファクトリーの基本的なメリットとして考えられます。
機械による作業以外にも、「従業員の作業状況」についての把握が容易であり、ミスの改善や習熟度の向上のために必要な分析材料が豊富に得られます。
(3)生産リソースの削減
生産工程の自動化・自律化によって人的な負担が大幅に軽減されるのはもちろん、材料や在庫の管理といった面でも大きな効果が期待できます。
受発注システムや在庫管理システムと、MES(製造実行システム)とを連携させることで、自動的に企業資源をめぐる状況が最適化され、各工程における資源ロスを解消することができるでしょう。
(4)多様なニーズへの対応
スマートファクトリー化の一つの狙いである「マスカスタマイゼーション」が可能となることで、製品の仕様についてのカスタマイズに細かく対応することができます。
たとえば、従来のように「オプション抱き合わせ」の販売方法では、顧客にとって「このオプションは欲しいけど、こっちは不要だなぁ……」という場面が多々ありましたが、細かな仕様変更に対応することで、顧客のニーズに正確に答える製品を提供することが可能となるでしょう。
スマートファクトリーのデメリット
(1)導入にあたってのハードルが高い
スマートファクトリーとしての設備を整えるにあたり、高い導入コストが必要となります。
ロボットやAI、IoT技術や各種ソフトウエアを揃えるにあたって、初期費用がかさむのはもちろんのこと、「どのようなものを採用すればいいのか」という選定も、専門家でなければ難しいと言えます。
近年では日立ソリューションズや富士通といった大手企業でも、スマートファクトリー化をサポートするサービスが増えてきていますので、そうしたサービスの利用も検討していくとよいでしょう。
(2)システム構築の難しさ
たとえば受注システムと生産工程を連携させる場合、CRM(顧客関係管理)やERP(企業資源計画)などのシステムと、MESとを紐づける必要があり、統合的なシステムの構築には現状について大幅な見直しや改修が要求されることになります。
さらに、開発部門やサプライチェーンなど、部門間のシームレスな連携を実現しようとするほど、システム構築の手間は大きくなり、組織そのもののあり方を全面的に転換する必要も生じてくるでしょう。
多くの場合、スマートファクトリーへの移行には数ヵ年規模での計画を要すると考えておく必要があります。
(3)メンテナンスのための人材確保
スマートファクトリーへの移行により、従業員に求められる能力はこれまでとは異質なものとなっていくと考えられます。人間の役割は主に「機器やプログラムのメンテナンス・管理」という内容へと移っていき、ロボットやIoT機器、ソフトウエアなどさまざまな最新技術を扱うにあたり、それぞれ専門的な知識が要求されるようになるでしょう。
「人間に求められる能力の変化」は日本政府にとっても大きな課題として捉えられており、学校教育においても2020年より「プログラミング」が必修化されました。そういった「新しい能力」を備えた人材が現れるまで、最新技術を扱える人材の確保は一つの課題です。
スマートファクトリー導⼊のポイント
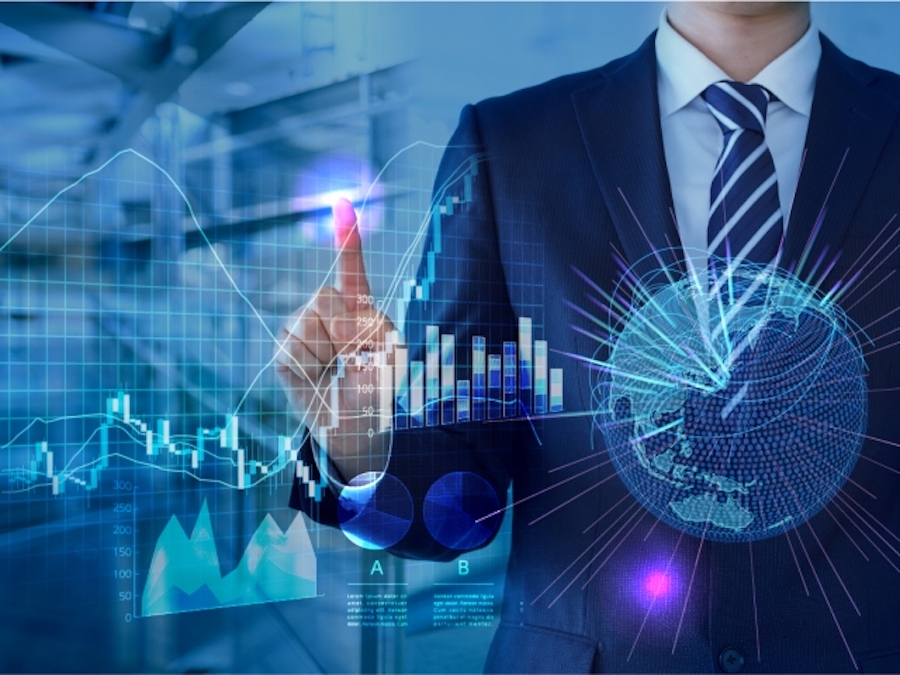
ここからは、スマートファクトリーとしての設備を導入し、環境を整備していくにあたって、どのようなポイントに留意しておくべきかをお伝えしていきます。
経済産業省が 2017年に発表した「スマートファクトリーロードマップ」では、スマートファクトリーへの移行段階として、三つのステップが提示されています。区分に準じて要点を解説していきます。
ステップ1:スマート化の構想策定
スマートファクトリーへの移行を決めてから、実際に導入を始めるまでの準備段階です。この段階において最も重要なポイントは、「ビジョンを明確に持つこと」と、「組織内で合意を形成し、方針を共有すること」の二点だと言えます。
まずは「明確なビジョン」について。スマートファクトリーへの移行によって「何を成し遂げたいか」を具体的にしながら、目標を数値として設定することが求められます。数値目標を掲げることで、実践段階において成果を随時確認し、フィードバックに活かすことができるでしょう。
さらに、目標に照らしながら、「業務のどの領域までをスマート化の対象とすべきか」「どのレベルまでスマート化を進めるべきか」といった具体的なプランを構想することが望まれます。コスト面も勘案しながら、専門家などの意見を伺うことも必要となるでしょう。
次に、「合意形成」です。スマート化によって生じうる従業員のネガティブな感情(仕事がなくなるのではないか、業務を常時監視されることになるのではないか等)を解消しながら、目的意識を共有していくことが重要です。
スマートファクトリーにおける従業員の役割を明示しつつ、管理体制によって従業員に生じうるメリットを掲げることで、大きな変化に対する一人ひとりの不安に応えていきましょう。
ステップ2:トライアル・システム導入
スマートファクトリーへの移行の成否を確認するために、業務の一部を試験的にスマート化していく段階です。
ここでは、将来的にスマート化が完了した後の全体像を見据えながら、そこへのステップを細分化して進めていくことが求められています。まずはリスクが小さく、効果を評価しやすい領域から試行を開始し、PDCAを繰り返しながら改善を図っていきましょう。
トライアルを実施する期間と対象についてあらかじめ整理し、段階を追ってシステムを拡張していけるような体制を整えておくことも重要です。数ヵ年にわたる計画のなかで、最終的なゴールを見据えながら、期間ごとに達成すべき目標を設定しましょう。
運用
スマートファクトリーとしてのシステムを対象範囲の全体に広げ、定着させていく段階です。
経済産業省のロードマップでは、このステップにおいて「導入効果の共有」を積極的に行うことが推奨されています。
経営者はもちろん、従業員も「このシステムでやっていけるのか」ということを懸念しているため、小さな成果もつぶさに評価・共有することで、従業員の不安解消やモチベーション向上につながります。
スマートファクトリーのシステムを「これからのスタンダード」として従業員の意識に根付かせ、さらにそのシステムを維持・改善していくための人材を育成することが、運用段階において重要とされています。
スマートファクトリーの導入事例
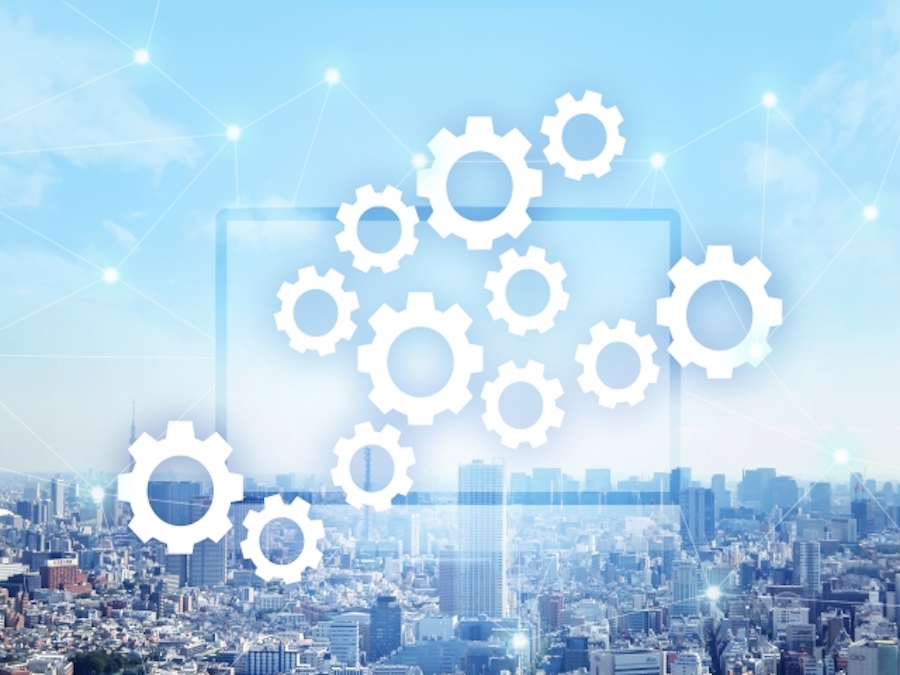
ここからは、すでにスマートファクトリーとしてのシステムを導入している企業について、その取り組みの概要を紹介します。
最も一般的な生産工程のスマート化だけではなく、開発・設計や受発注システムのスマート化の事例も取り上げながら、スマートファクトリーの持つ多様な可能性についてお伝えしていきます。
生産工程への導入事例
建設機械の生産を手掛ける「株式会社小松製作所」は、「KOM-MICS」というスマートファクトリー化の改革を進め、2019年には「第8回ものづくり日本大賞」において製造・生産プロセス部門の内閣総理大臣賞を受賞しています。
KOM-MICSは、グループ会社を含めた生産工程の「見える化・つながる化」を目指したもので、同社やその協力会社における生産設備にIoT技術を導入し、サーバー上に集められたデータをアプリ上で確認できる、というシステムを基本としています。
生産設備の稼働状況や工作機械ごとの出来高はもちろん、加工工程における「切削抵抗」などの専門的なデータも詳細に蓄積することで、機械の適応制御をリアルタイムに行えるシステムの開発に成功しています。結果としてコマツグループ全体における品質の安定化や、サイクルタイムの大幅な低減が実現されているとのことです。
(参照:「コマツ|生産現場“つながる化”KOM-MICS」)
開発・設計段階への導入事例
通貨処理機の専門メーカーである「ローレルバンクマシン株式会社」は、新製品開発において「企画段階で見込んでいた原価と、設計終了時で判明する実際の原価が乖離してしまう」という課題を抱えていました。
企画段階においてコストを明確に把握するため、同社はコストシミュレーションシステムの開発に取りかかり、可視化ツールとして図面や工程表、部品データなどを紐づけながら一元的に管理できる「Visual-BOM」を導入しました。
開発に三年近くを要したコストシミュレーションシステムが完成してからは、BOM(部品表)やPDM(製品情報管理)、CADの自律的な連携により、企画段階において見通せなかった原価をより的確に把握できるようになりました。さらに副次的効果として、コスト計算の作業が自動化されることで、最大1ヵ月分の工数削減にもつながったとのことです。
(参照:経済産業省|「2020年版ものづくり白書|第1部第1章第3節 製造業の企業変革力を強化するデジタルトランスフォーメーション(DX)の推進」)
顧客管理・受発注段階への導入事例
油圧機器の製造や板金加工を手掛ける「株式会社今野製作所」は、カスタムオーダーへの柔軟な対応や、新規顧客の開拓を目的に、三社合同のプロジェクトにおいて「見積もり」「工程進捗」のシステムを共有して運用しています。
自社内で営業・設計・購買・管理の四部門をシームレスに連動させながら、自社だけで対応できない加工作業については、リアルタイムに金額や進捗状況を確認できるシステムを用いて他企業と緊密に連携することで、業務ロスを大幅に低減し、顧客への情報開示もスムーズかつ正確に行うことが可能となりました。
今野製作所はこのプロジェクトに先立って、自社内で生産管理システムを開発しており、在庫や受注状況、部品データなど、受注から購買、生産、出荷までを一元的に管理しうる体制を整えていました。
スマートファクトリーへの移行を自社内に留めることなく、他企業の連携のため拡張していくことで、双方にとって有益なシステムを構築しうる好例と言えるでしょう。
(参照:「経済産業省|平成28年度スマート工場実証事業 成果報告会|今野製作所」)
まとめ
ロボットやAI、IoT技術は、とりわけ製造業との相性がよく、綿密な計画にもとづくスマートファクトリーへの移行は、まさに革命的な変化をもたらす可能性を持っています。
経済産業省をはじめ、政府が率先してスマート化を推奨していることからも、これから「産業構造そのものの転換」がなされていくことは想像に難くありません。
スマートファクトリーへの移行は、計画から実際の運用まで数ヵ年を要する大規模な変化となります。なるべく早い段階から、導入について検討し、構想段階へと移っていくことが望まれます。
まずは既存の設備に追加できる形のセンシング機能など、リスクの少ないところから試験的に導入し、効果を確かめてみるのもよいでしょう。
RANKING ランキング
- WEEKLY
- MONTHLY
UPDATE 更新情報
- ALL
- ARTICLE
- MOVIE
- FEATURE
- DOCUMENT